Types Of Potting Materials For Electronic Protection
- qinglongdatech
- May 13
- 4 min read
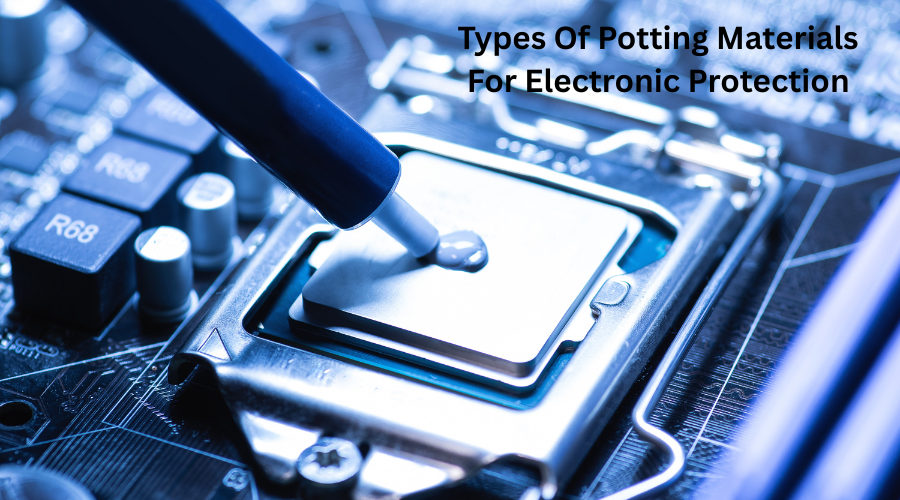
When it comes to protecting sensitive electronic components from moisture, dust, vibration, and heat, potting materials play an essential role. These materials envelop the components, forming a protective layer that enhances durability and longevity. Whether you're an electronics hobbyist or working with a professional electronic potting compound manufacturer, knowing the various types of potting materials is vital for choosing the right one for your application.
In this blog, we'll explore the most common potting compounds used in electronics, discuss their pros and cons, and guide you on which material suits different electronic environments. This is a must-read for anyone seeking reliable, long-term protection for electronic devices.
What Is Electronic Potting?
Before diving into specific types of potting materials, let's quickly recap what electronic potting actually is.
Potting is the filling procedure of an electronic assembly with a solid or gel-like compound to provide insulation and protection. The goal is to shield the components from environmental factors such as:
Moisture and humidity
Chemical exposure
Mechanical shock
Thermal cycling
These compounds are usually applied in liquid form, poured over or around the components, and then cured to form a solid, protective casing.
Why Is Potting Important in Electronics?
Potting isn't just about making a product more rugged—it's about ensuring reliability and safety. Here's why manufacturers and engineers consider potting indispensable:
Improves the lifespan of components by reducing exposure to damaging conditions
Improves electrical isolation, reducing the risk of short circuits
Dampens vibration and mechanical stress
Discourages tampering with the internal components
Improves thermal management in heat-sensitive applications
Now let's look at the different types of potting materials and their unique characteristics.
1. Epoxy Resins
Epoxy is one of the most widely used potting materials in the electronics industry due to its excellent adhesion, rigidity, and resistance to moisture and chemicals.
Advantages:
Strong and durable
Excellent electrical insulation
Good chemical resistance
Handles high heat environments well
Disadvantages:
Brittle once cured
Can be difficult to remove if rework is needed
Longer cure times than other materials
Best For:
High-voltage transformers, automotive control modules, and industrial-grade sensors.
2. Polyurethane Compounds
Polyurethane is often selected for applications requiring more flexibility than epoxy. It provides good shock absorption and is ideal for environments where components may be subject to vibration.
Advantages:
Flexible and impact-resistant
Good thermal cycling performance
Faster cure times available
Less brittle than epoxy
Disadvantages:
Lower chemical resistance
May degrade under prolonged UV exposure
Best For:
Consumer electronics, LED drivers, and portable devices.

3. Silicone Compounds
Silicone potting materials are prized for their thermal stability and flexibility over a broad temperature spectrum. They remain effective in extreme heat and cold, making them designed for use in the aerospace industry and automotive applications.
Advantages:
Excellent thermal resistance (up to 200°C or more)
Soft and pliable even after curing
High dielectric strength
Suitable for sensitive components
Disadvantages:
Generally more expensive
Lower mechanical strength compared to epoxy
Best For:
High-temperature applications, medical electronics, and sensors are exposed to outdoor conditions.
4. Acrylic Compounds
Acrylics cure rapidly and are often used in low-cost or fast-production environments. While not as strong as epoxy or silicone, they're a great choice when speed and ease of use are priorities.
Advantages:
Fast curing, even at room temperature
Moderate flexibility
Easy to apply and remove
Disadvantages:
Lower durability
Less resistance to extreme temperatures
Best For:
Low-power devices, battery packs, and prototypes.
5. UV-Curable Compounds
UV-curable materials offer instant curing when exposed to ultraviolet light, making them suitable for high-speed manufacturing lines.
Advantages:
Instant or rapid cure
Low shrinkage
Excellent for small or delicate assemblies
Disadvantages:
Requires UV exposure for curing (not ideal for opaque components)
Limited depth of cure
Best For:
Miniature electronics, circuit boards, and optical devices.
How to Choose the Right Potting Material
When selecting a potting material, it's essential to consider a few key factors:
Thermal requirements: Will the device experience high heat?
Flexibility: Does it need to absorb shock or vibration?
Chemical exposure: Will it be exposed to oils, solvents, or moisture?
Electrical insulation: Are you protecting high-voltage circuits?
Ease of repair: Will you need to remove or rework components?
Also, working with a reputable manufacturer can help ensure you get a formulation that meets your specific performance and environmental requirements.
Environmental and Safety Considerations
While potting materials enhance product performance, some can present environmental or health hazards if not handled properly. Always follow:
Proper ventilation guidelines
Manufacturer safety data sheets (SDS)
Curing and disposal protocols
Eco-friendly alternatives and low-VOC (volatile organic compounds) formulations are becoming more available, making it easier to maintain sustainability without sacrificing quality.
Conclusion
Selecting the right potting compound is crucial to the performance, safety, and longevity of your electronic components. From epoxy's rugged strength to silicone's extreme temperature tolerance, each material brings its own benefits to the table.
If you're unsure which compound is best for your application, consult with a knowledgeable manufacturer early in the design process. They can guide you toward the most suitable formulation that meets your technical and regulatory requirements.
In the end, choosing the right potting material isn't just about protection—it's about ensuring your product stands the test of time.
FAQs
Q1: Can I remove potting compound from electronics?
Yes, but it depends on the material. Epoxy is difficult to remove, while silicone and acrylics are more manageable. Specialized solvents or thermal methods may be needed.
Q2: Does potting improve heat dissipation?
Some potting compounds are designed with thermally conductive fillers that help transfer heat away from components, improving overall thermal management.
Q3: Are all potting materials waterproof?
Most potting materials are water-resistant, but not all are 100% waterproof. For marine or high-moisture environments, silicone or specially formulated epoxies are best.
Q4: What's the difference between potting and encapsulation?
Potting usually involves filling a case or shell with compound, while encapsulation often fully surrounds the component in a mold or enclosure.
Q5: Can I use potting compounds for outdoor electronics?
Yes! Silicone and polyurethane compounds are excellent choices for exterior application due to their resistance to moisture and temperature changes.
Comments